“From the workshop to the office, we work together here”
working at (3)
Eldrichd van Eijma (25) and Dominique van Nes (25) started at Mennens Cleanroom Cranes in 2022. They soon noticed that there was plenty of room for growth and development, and that their individual input was valued. While Eldrichd is gaining experience as a production worker and technician in the workshop, Dominique is learning every day in the office as an administrative assistant. They now share with us their thoughts on their experience.
Before starting here, Eldrichd worked at the Mennens site in Dongen, a sister company of Mennens Cleanroom Cranes.
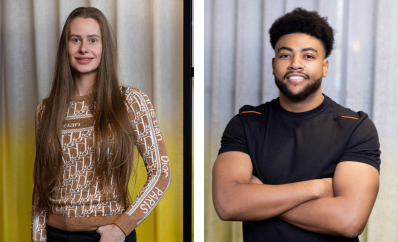
He recounts: “In Dongen, I repaired electric hoists and steel cables. After a while, I wanted to switch to field service. I told that to my supervisor. We agreed that I would first join Cleanroom Cranes for a while, here in Eindhoven. And I would then move on to field service. But I like it here so I decided to stay.”
Dominique has also been a valuable member of the Cleanroom Cranes team since March 2022. Her work as an administrative assistant is extremely varied. “Among other things, I keep track of purchases and I check and approve purchase invoices. I also gather together all the technical documents for the cranes, such as 3D drawings, supplier certificates and manuals. I use that to compile files and send them to clients. I also prepare purchase orders, keep track of office supply stock and ensure that progress billing runs smoothly. In addition to that, I prepare the transport documents for crane shipments.”
“I have a lot of freedom to organise my own work”
Crane construction
While Dominique makes sure the administration runs perfectly, Eldrichd sees to it that the construction of the cleanroom cranes goes ahead smoothly and professionally. “I get a drawing from the engineers on how the crane is to be constructed. Here, I have a lot of freedom to organise my own work, as long as it is done well and by the deadline. Sometimes the engineers draw something that ends up not being such a good fit. Then I consult with the engineers and we work together to figure out the best way of doing it.”
“The crane I built in Eindhoven will be installed in Korea”
Every detail has to be perfect
When building a cleanroom crane, everything has to be perfect, explains Eldrichd. “These are special cranes for cleanrooms. The cranes are used for tasks like lifting heavy machines that make computer chips. Their construction is subject to strict regulations and high-quality standards. The same is true for customer installations. If we forget anything at all, or one small component is not right, the entire installation will fail. That’s why we test every single crane on a test frame before it heads out. We check to make sure every function is working 100% correctly.”
Off to South Korea
Soon, Eldrichd will be joining the crane installation team for the first time, at a customer site in South Korea. “It will be very cool to install the crane I built in Eindhoven in Korea myself. I’ll be doing this alongside an experienced colleague, who’ll be showing me the ropes. After the installation, we’ll test the crane in front of the customer.”
“The workshop and office form a single whole”
Fast-growing company with growth opportunities
Why did Dominique choose Mennens Cleanroom Cranes? Dominique: “It’s a fast-growing company that offers you plenty of opportunities to develop yourself and grow into another position. I’m now being considered for a position with more project-related responsibilities. I think that would be a great next step.”
Clean, tidy and very welcoming
For Eldrichd, in addition to the job itself, the working environment and atmosphere were crucial in choosing Mennens Cleanroom Cranes. Eldrichd: “It’s always clean, tidy and very welcoming here. Really different to a lot of other workshops. One thing I like is that the workshop and the office form a single whole. These are often separate worlds. Here, we walk right in to see the engineers, project managers and management. And the same goes the other way round.”
Dominique agrees with Eldrichd. “I talk as easily to the director as I do to my office colleagues, the technicians and the engineers. We always try to have lunch together as often as we can. Then we all sit together at a long table, which I enjoy very much. On Fridays, I order something nice for whoever wants it. Sometimes sandwiches, or other times some chips. On Friday afternoons, we stop a little earlier and get together for some drinks. All in all, the atmosphere is great and everyone treats each other with respect.”
Will you be joining us as a new colleague?
Do Eldrichd and Dominique’s experiences appeal to you? Explore our vacancies and apply with us. We would love to meet you.
Interested in more experiences from our team?
Read the interview Engineering requires creativity and smart solutions with Timo and Connie from the engineering department.
Or read the interview A quick introduction to all the aspects of engineering with Yannick and Danny.