VGI-Willems RVS Machinebouw, located in Hapert, Brabant, has been a partner in stainless steel machine construction, sheet metal work, and frame construction for over 30 years. For the assembly of valuable stainless steel machine parts for a client in the semiconductor industry, VGI built a cleanroom. Mennens Cleanroom Cranes (MCC) developed a custom cleanroom crane for this purpose.
In short
-
VGI builds a new cleanroom to assemble stainless steel machine parts.
-
VGI's client imposes strict cleanliness standards on the assembled parts.
-
The (heavy) machine parts must also be moved cleanly.
-
VGI therefore enlisted MCC for a custom cleanroom lifting solution.
About VGI-Willems RVS Machinebouw
VGI supports organizations in various industries with stainless steel sheet metal work and frame construction. They assemble and manufacture stainless steel machines for clients in the food, transport, pharmaceutical, and semiconductor industries, among others. Examples of machines assembled by VGI include cutting and sorting machines, vibrating sieves, and conveyor belts.
The factory in Hapert is fully equipped with, among other things, sheet and tube laser machines, a machining department, welding, and stainless steel finishing. VGI has several assembly areas for building sub-assemblies into complete production lines.
“Based on the calculations of the architect and constructor and our wishes, Mennens Cleanroom Cranes provided the necessary specifications of the crane. And they came up with a custom design.”
Marco van Geel
Owner VGI Group
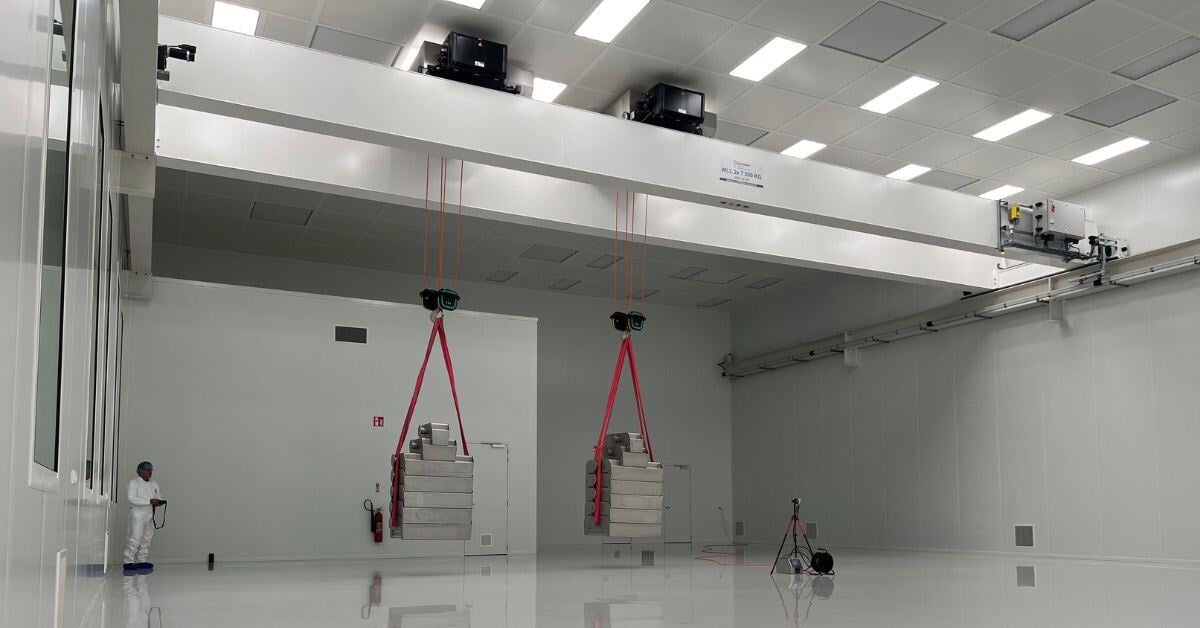
Assembling machines dust-free for cleanroom applications
Some time ago, VGI was approached by a player in the semiconductor industry. Marco van Geel, owner of the VGI Group, explains: “This party asked if we wanted to be their partner for the assembly of their stainless steel machines. What is special about this is that these machines must be delivered clean and dust-free according to a specific cleanliness standard. The standard determines, among other things, the maximum number of (dust) particles allowed per square decimeter of the product surface.”
Building a cleanroom
To be able to serve clients with such high cleanliness requirements in the future, VGI built a cleanroom. Marco: “A lot was involved in this. It soon became clear that we needed a cleanroom crane for moving the machine parts. This also has to be done cleanly, but a traditional crane has a hoist with a steel cable that needs to be lubricated. This generates a lot of dirt. So this was not an option.”
Trust
Mennens Cleanroom Cranes was not unknown to Marco. “They have a lot of experience and proven solutions for clean lifting, also in the semiconductor industry. I had already seen their cleanroom cranes in operation at one of our clients' locations. That gives confidence and that was important to us: this lifting solution had to be good. Of course, we also looked at other parties. But during the first conversation with MCC, the feeling was immediately right. The choice was made quickly.”
Specifications and design
Marco explained that MCC was involved from the early stages. “Based on the calculations of the architect and constructor and our wishes, MCC provided the necessary specifications of the crane. And they came up with a custom design.”
Dyneema rope hoist
The lifting solution was found in an overhead crane with a span of 17 meters and two hoists of 7.5 tons each, totaling 15 tons. Marco: “This allows us to lift and position the heavy machine parts safely, cleanly, and very precisely. The hoists are equipped with a Dyneema rope hoist. This rope has very strong fibers and releases virtually no particles.”
“My compliments to the MCC team. They approached this professionally."
Marco van Geel
Owner VGI Group
Material choice and precision
Every material choice within the crane design is made by MCC with precision and based on years of experience. The crane is treated with a special cleanroom coating. The rails on which the wheels move and the wheels themselves are made of stainless steel so that there is hardly any particle emission during the crane and trolley functions. Moreover, the crane is frequency-controlled, which allows for very precise positioning. VGI also has the option to lift synchronously with the two hoists, which is important when positioning delicate machine parts.
Challenge: installation
The final installation on site proved to be a challenge. Marco: “My compliments to the MCC team. They approached this professionally. The installation of the cleanroom crane took place while our cleanroom was already partially under construction. The overhead crane was too large to make the necessary turn for installation on the crane runway within the cleanroom. MCC developed a lifting plan to still position the crane correctly in the space. The crane ultimately arrived in parts, was assembled in parts here, and installed in the correct place.”
Validation: spectacular test results
For VGI, it is crucial that they can deliver the stainless steel machines to the client according to cleanliness standards. The lifting solution had to perform within the required ISO classification. To be sure of this, the hoist was validated on-site at VGI by an independent expert in contamination control, on MCC's advice.
Marco explains: “The crane was validated with advanced measuring equipment in our own cleanroom. We simulated our lifting process with the crane from light to the heaviest conditions (crane driving, trolley driving, and lifting simultaneously, under full load). Then, the number of particles released was measured during each crane action. How does the crane perform when it starts moving, moves, and comes to a stop? What is the effect when employees walk through the space at the same time? The results were spectacular. The cleanroom crane performs excellently even under ISO 6. To give an idea: in a certain situation, 184 dust particles were measured, where the standard allows 35,000.”
Clean lifting with a proven solution
The cleanroom crane is now operational. Marco looks back positively on the collaboration with Mennens Cleanroom Cranes: “Thanks to the crane, we are able to assemble very valuable stainless steel machines super cleanly, according to our client's requirements. And if necessary, the construction of our cleanroom allows for expansion with another 15-ton cleanroom crane. After all, more parties require cleanliness standards for the assembly of their stainless steel machines. That we can now provide for this is fantastic. So if we expand in the future, we will certainly know where to find Mennens Cleanroom Cranes again.”
More information
Curious about the added value of a cleanroom crane for your organization? Our experts are ready to assist you. Contact us via our contact form. Or contact us via +31(0)88 425 83 00 or sales@cleanroomcranes.nl.